Rheological Testing; Unlocking insight on chemical and materials product properties and performance
Rheological testing is a fundamental tool in materials science and chemical product development, offering valuable insights into the behavior of fluids and solids under varying conditions. Rheology, the study of how materials flow and deform, is critical for understanding the intricate properties of substances. Our specialized rheology research laboratories analyze polymeric materials, liquids, adhesives, and various other samples, helping to address key challenges across a multitude of industries.
One of the primary applications of rheological testing is optimizing the molding process for polymers. Our experts comprehensively assess the rheological properties of polymers to ensure correct processing with minimal product degradation. This not only enhances product quality but also reduces production costs by minimizing material waste. We employ a diverse array of rheological tests, ranging from single point tests to variable shear-rate tests, to accurately gauge polymer viscosity.
Rheological characterization is conducted under various shear, tensile, and extensional conditions, providing data that serves a myriad of purposes, including quality assurance, product development, and a deeper understanding of material performance. Whether it's analyzing oils, dispersions, emulsions, solutions, or slurries, our fluid rheology tests provide critical information about material behavior. For instance, in the cosmetics industry, rheological testing can help formulate the perfect lotion texture or assess the flow properties of various emulsions. In the medical device sector, understanding the viscosity of dermal filler injectable products can help improve formulation to optimize clinical performance.
Fluids analyzed include
- Oils
- Dispersions
- Emulsions
- Solutions
- Slurries
- Resins
- Lotions
- Polymer melts
- Greases
Fluid Rheology tests are performed while the polymer is in the melt phase or while the polymer has been dissolved in a solvent for Intrinsic Viscosity and Relative Viscosity.
Solids analyzed include
- Polymer plaques
- Elastomers
- Rubbers
- Fibres
- Films
- Composites
- Thermoplastics
- Thermosets
- Molded articles
- Adhesives
Rheological tests can measure the viscosity of a polymer ranging from single point tests to variable shear-rate tests.
Rheology tests include
- Frequency sweeps
- Temperature ramps
- Intrinsic viscosity and relative viscosity
- Melt flow rate (MFR) and Melt Flow Index (MFI)
- Capillary rheometry
- Creep (flow under a given force or stress)
- Stress relaxation (change in force for a given deformation)
- Thermal stability
- Melt viscosity
Many of these techniques fall under the umbrella of Dynamic Mechanical Analysis (DMA). These DMA tests often provide a mechanical fingerprint for a material. Properties such as Tg, the breadth of Tg, secondary transitions, crosslink density, and many others can be determined using DMA.
Contact our experts to discuss the most relevant way to use rheology for your application. Ultimately, a better understanding about your material’s properties will enable you to proceed towards the creation of a product with improved performance. Intertek’s rheology laboratories are located in Europe and North America.
Rheology testing:
Two major rheological analysis methods are available for the characterisation of creams/pastes and semi-solids, such as Controlled Stress Rheology (Rheometrics SR500) to predict properties such as shelf life/ease of application and stability - sedimentation rate - performed over a variety of test temperatures) and Controlled Strain Rate Rheology (Rheometrics ARES, RDAII).
We also provide Dynamic oscillatory rheology can also be performed which provides much more information on the microscopic structure of viscoelastic materials (such as creams and pastes) as well as further tests to determine the limit of the linear viscoelastic response, dispersion quality and also material thixotropy, elasticity and stiffness values.
Hyaluronic acid (HA) gels are used by dermatologists and cosmetic surgeons as dermal fillers, which when injected into the skin, can ‘lift’ wrinkles and improve facial appearance. The different processes used in their manufacture and formulation yield products with unique physical characteristics that play an important role in predicting their clinical performance and lifetime of benefit perceived by the patient.
Understanding the relationship between the particle size and particle size distribution of crosslinked HA gels with the viscoelastic behaviour of the gels themselves can help manufacturers develop unique property/microstructure relationships that can help clinicians in achieving desired results for a variety of patient needs.
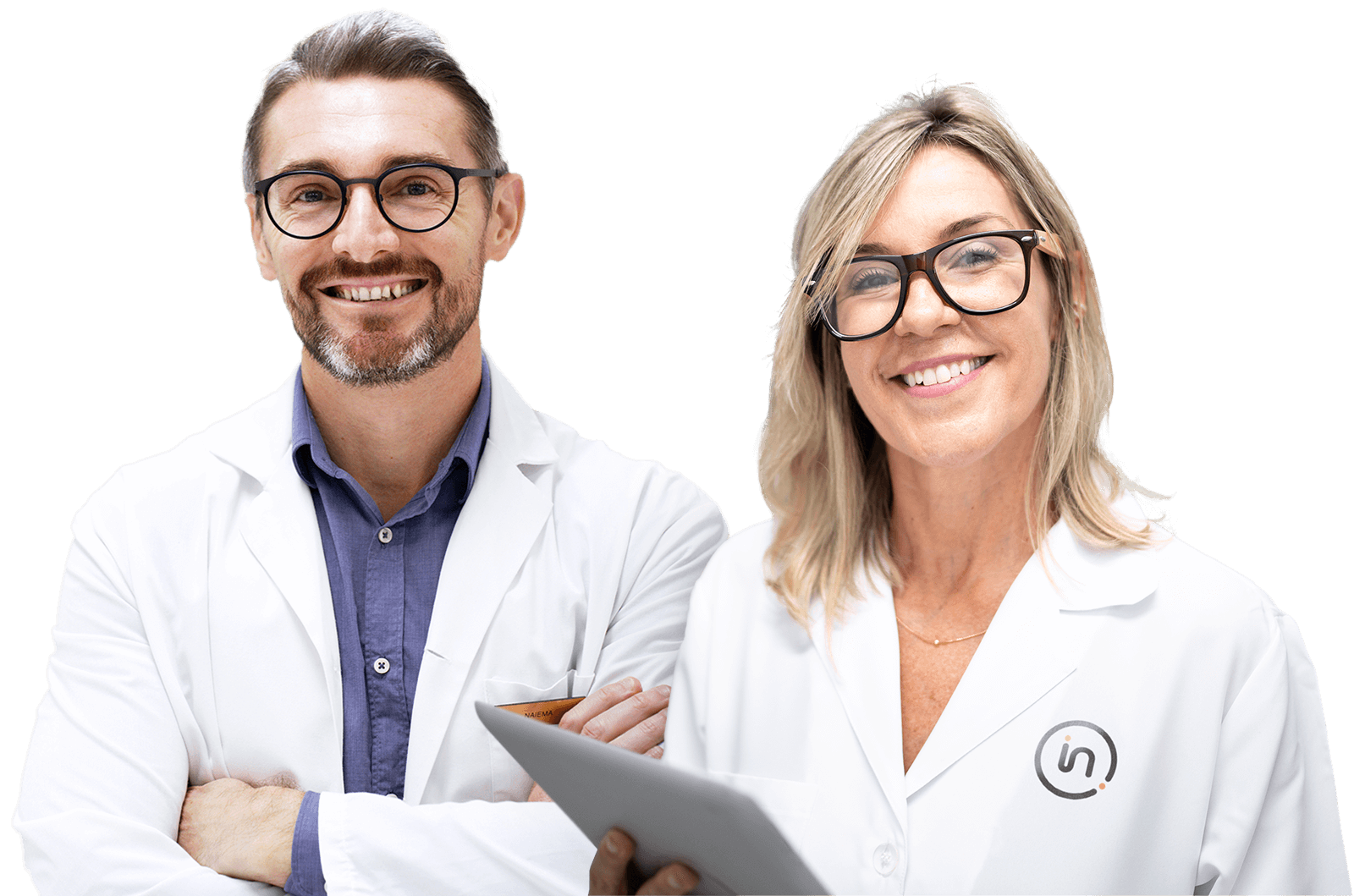