Flying Blind: New Minerals Processing Technologies and Plant Design - Part 2
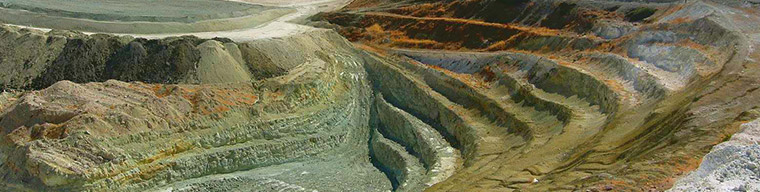
11 Nov 2014
New minerals processing techniques may offer you increased efficiency or may saddle your project with a white elephant, and finding out ahead of time is not always straight forward.
vsi crushers use a high speed rotor to fling the feed material outwards where it impacts with a solid, stationary wall. the shock experienced on impact breaks the mineral particle along its grain boundaries, which should lead to less composite particles and improved separation efficiency in subsequent unit processes. key parameters are the velocity obtained and distance to the chamber wall. while the distance to the chamber wall cannot be faithfully replicated at the lab scale, vsi crushing can be simulated in pilot scale plants. there is a cruel convergence of our ideal crusher product characteristics and the vsi’s weaknesses though; exactly those projects which would benefit from particles being separated along grain boundaries, specifically complex ore bodies, produce inordinate amounts of fines when vsi is applied. the fines stick to the inside of the machine, gumming up the works and preventing efficient crushing. moisture also exacerbates the issue, which is often in ample supply due to dust reducing sprays in the primary stage crushers. these effects are difficult to quantify in pilot scale trials, and unfortunately, i’ve had first-hand experience on a project where it was only during plant commissioning when it was realized that vsi was not well suited to their application.
isamills are without a doubt one of the greatest innovations in mineral comminution since the sledgehammer. they allow energy efficient grinding down to a few microns, which make the difference between a massive deposit of unextractable minerals in the earth, and a lucrative mine with decades of production. however, as they are such a new and complex technology, there are many variables that can determine if and how they ought to be used in a given application. the isamill consists of a stationary cylindrical outer shell mounted horizontally. unlike other mills, the isamill is filled completely with relatively dense slurry with no head space of air. inside, there are rotors mounted on a central axle that spin at high speed, together with a grinding medium. the viscous slurry along with the grinding medium is dragged by the rotors inducing attrition as the particles rub against one another and the hard medium material. simple trials with bench top isamills can help to select a grinding medium, and determine the optimum slurry density, rotor speed and mill throughput. there are other variables however, such as the mill liner material, rotor shape and design. these require more complex customized trials, so arriving at an optimum final design can require quite a substantial effort.