Key considerations in future proofing the product safety supply chain
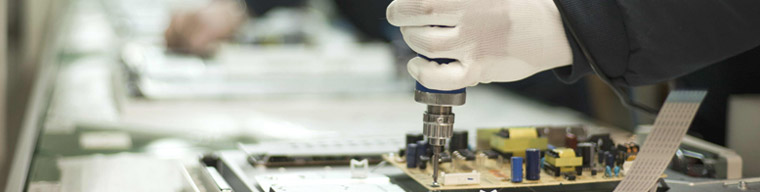
06 Jan 2015
There are multiple considerations behind the development of a robust product safety supply strategy and here we explore the main areas when developing leading organisational assurance processes.
more and more we are hearing from our clients how the impacts of global competition and new emerging markets are driving a manufacturing price war. retailers and suppliers are being forced to source or consider products from less expensive, and more often than not third world destinations, where product safety standards and appropriate legislation may be in their infancy. new markets such as bangladesh, vietnam and india are posing strong competition to the previously unrivaled manufacturing economies of scale in china. this is just one trend that emphasises the growing need to future proof your supply chain.
there are multiple considerations behind the development of a robust product safety supply strategy; below we’ve outlined our top five when developing leading organisational assurance processes:
build shared commitments with your supplier
investing time early on in getting to know your potential supplier as well as establishing clearly aligned expectations and deliverables will enable you to build a more successful supply relationship. if effective due diligence has been conducted during the screening process, you should feel confident that your supplier shares your commitments in meeting regulatory compliance, safety and environmental targets. it also helps to ensure efficiency and quality throughout the supply chain.
conduct approval audits
engaging a third party test agency such as intertek can assist you to determine if your supplier is able to deliver a consistent product to the same quality, environmental and safety standards required by your internal policies and compliant with your end users’ local consumer laws. other factors such as worker qualifications, working conditions and facilities management can be qualified during this process.
a good approval audit will evaluate suppliers’ capacity across factors including: cost, quality, innovation, risk and corporate social responsibility – ultimately providing the assurance to appoint or reject a supplier.
maintain brand integrity
making claims that your product is better than another need to be substantiated, or legal action may ensue. when marketing or advertising a product, you must describe them according their intended design and use. marketing strategy should take into account:
- its key safety aspects
- what it has been designed for
- who will use it
- how they will use it.
manage reputation through proactive two way communication
in this hyper connected world, particularly with the emergence of social media, you want to make sure you are aware of what is being said about your brand and have a strategy in place to reciprocate when, not if, an issue arises. in australia for example, organisations are required to comply with the australian standard as/iso 10002:2006, which is entitled customer satisfaction—guidelines for complaints handling in organisations. this standard provides organisations with advice on the complaints handling process, including planning, design, operation, maintenance and improvement.
additionally, another trending issue is that of corporate social responsibility (csr), which is now very real in the minds and resulting purchasing habits of consumers. ensure you are confident in the reliability of your manufacturers and live up to your csr commitments.
follow industry best practice
proactive alignment with risk regulators such as the australian competition and consumer commission (accc) who monitor and benchmark best practices globally will support your organisation’s key decision makers in increasing their understanding of potential risks and pitfalls.
by consistently maintaining and developing in-house knowledge and awareness of international regulations and guidelines you are better placed to establish a mitigation strategy to identify unsafe goods before they reach the market.
there is no doubt in my mind that organisations who invest in appropriate quality and assurance methods throughout the entire product development process will have fewer safety problems, accidents, law suits and recalls. proactive management is the key and ultimately the safety of consumers will result.
recently, intertek consumer goods australia hosted a series of product safety information forums, which provided manufacturers, importers and retailers the opportunity to discuss leading assurance practices, as well as their hear first hand their obligations under australian consumer law. click here to access the event resources.