On Target with the Right Information at the Right Time
24 Aug 2021
Demystifying a Custom Test Program
No matter the product or component, you need information to make the decisions. But to make effective decisions, it must be the right information, available at the right time, and it must be usable. A custom test program can help ensure the correct information is provided by the best evaluations and completed in time.
A custom test program requires three key considerations. The first is fit: will the information provided help answer the question. Consider what the question is and what information will answer it. Next, ensure this information is available when it is needed. Different tests have different durations so it is important to think about when the question will need to be answered. Finally, ensure that the information is usable and in a form that stakeholders can understand and trust.
Fit
Questions leading to testing tend to fall into three categories: business or engineering assumptions needing validation, variables needed to inform decisions, or analysis/exploration to discover opportunities. It is important to understand what the question is and what piece of information will help get the necessary answers. Then, figure out what the testable statement is, what needs to be measured/controlled, and how the evaluations will be done.
In short, start with the information needed, then think about how to get it. This could include any number of tests such as:
- Failure analysis: The investigation into determining why failure occurred, either unexpectedly or at a point in the lifecycle. This could mean fractures; malfunction of a component, subsystem, or system; visual defects; or other unexpected issues that causes product dissatisfaction.
- Environmental testing: Exposing materials, components, sub-systems, or full products to conditions that may be found at end-use stages to test endurance. This might include temperature, humidity, radiation, sunlight, salt spray/mist, dust, or chemicals.
- Material assessments: Measuring the physical, chemical, or mechanical properties of materials. Assessments may look at physical properties, density, thermal expansion, chemical properties, molecular make up/structure, contaminants, flammability, and more.
- Mechanical testing: Examines properties such as tensile strength, elongation, durability, hardness, abrasion, compression, tear, peel, pull, and impact. This type of test is often done in conjunction with environmental exposures.
- Vibration testing: Exposing a product to vibration energy to measure or demonstrate life. Similar to mechanical durability, this type of test is often done in conjunction with environmental exposures, as well as functional testing.
- Electrical performance assessments: Measures performance at the system, sub-system, or component level for information on concerns like current, voltage, power draw, functionality, temperature, or resistance changes. This is often done in conjunction with environmental exposures, vibration, and durability.
- Accelerated Stress Testing (AST): A set of tests with a highly focused information goal, using elevated stress levels to achieve faster results. These tests do not demonstrate compliance to a standard, they provide information to help engineers or managers make specific decisions.
- Lighting: Assessing characteristics like light quality, brightness, color, pattern, and durability.
- Other tests as needed.
Availability
It is not enough to have a test produce the right information; the information also needs to be available at the right time. This is especially true when dealing with a warranty issue, development timelines, legal matters, or anything time sensitive. Each test has a different run time. For example, AST can take about a week to complete, after planning and set-up. Failure analysis can take multiple weeks, perhaps longer depending on complexity. Lighting testing can range from a few days to multiple weeks. It is important to be clear on the time frame for test completion, as well as how long it will take to interpret the data and make decisions. A test that produces perfect information two weeks to late is not as valuable as an approximation that is available in time to make a decision.
Usability
To ensure that information is usable and trustworthy, keep the stakeholders in mind. Designers will have different needs than compliance. Regulators have different requirements than consumers. And retailers/customers have different needs than executives. Keeping who will use the information in mind can help ensure it is presented in the best form. A test report may work for an engineer or regulator, for example, whereas a retailer or consumer simply needs an accreditation mark or public listing. How do you get to the needed information? How do you present it? Be clear on who your end audience is.
A custom test plan should clearly capture the key decision(s) you're trying to make with clear timing, appropriate evaluations and useful information. It can be a valuable tool for a number of decisions. Get additional insights into custom test plans, including examples and the process, by downloading our webinar recording.
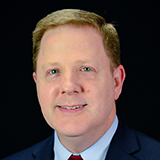
Alex Porter,
Global Director of Engineering
Alex Porter is the Director of Global Engineering for Intertek and has been with the company since 1992. He has been developing accelerated testing methods for mechanical components and systems since 1996 and holds three patents related to accelerated testing equipment and authored more than 40 articles and technical papers on accelerated testing. Porter is the author of the book "Accelerated Testing and Validation" (Elsevier, 2004) and teaches a class for SAE based on the book. He is a member of SAE, holds a B.S. in aircraft engineering, an M.S. in mechanical engineering, and is a professional engineer in the state of Michigan.
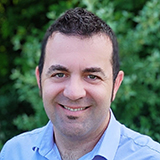
Dorian Bako,
Department Manager
Dorian Bako is the Department Manager for furnishings durability and electrical safety. He is has been with the company for 17 years, with many of those years directly linked to furnishings testing. Bako has experience in test standards such BIFMA, KCMA, BHMA, SEFA, ASTM, EN, as well as UL and CSA. He holds a B.S. in mechanical engineering from Hope College in Holland, Michigan.