Why Product Certification Could Boost Your Sales
20 Oct 2022
Learn how product certification plays an integral role in the success of your building products
A quality building product certification could make or break your product. As many marketers know, a third-party "seal of approval" can send sales skyrocketing. Building product certifications go even deeper and can elevate an ordinary product to a trusted brand. Third-party certification means you've invested the time and money to meet a building code, local jurisdiction requirement, or an industry standard. Certified product manufacturers have not only passed the appropriate tests but have taken it to the next level by acquiring the correct certifications. In short, certifications provide the building owner or end-user with evidence that a product meets the requirement and is fit for purpose.
There are differences between certification and testing. Testing is a critical part of the certification process, as it determines product performance. Certification ensures that the product performs consistently at all times. Certification means that a product that leaves the factory will meet certain performance criteria, assuming it is installed the way it was in the test lab. To maintain certification, the production line must be checked annually.
Certification is a long-term relationship. Intertek excels in following products throughout their life cycle and, in some cases, can be in clients' facilities for decades. Certification can get complicated when product performance or details change over time. The manufacturer may change materials used in the product due to supply shortages, packaging may have changed, products can be updated, or any number of other small details. Companies that offer third-party certification, like Intertek, should have the capability and responsibility to quickly respond to these changes and adapt to the client's evolving needs.
If a product does change over time, it is the responsibility of the client to recertify or update the certification. However, having a good working relationship can minimize unnecessary costs and provide the best path forward to maintain the product's certification.
Steps to Product Certification
The certification process with Intertek starts with truly understanding the client's product offerings, business objectives, and market conditions. The goal with each client is to help companies obtain the proper certification centered on the client's needs and time-to-market goals. The following six steps outline the typical process Intertek goes through with each client.
Step One: END GOAL
When customers are ready to certify, we start by focusing on their end goal. It's our job to understand what markets they plan to enter, the range and complexity of the product, sustainability concerns, and a range of other market needs.
Step Two: DETAILED TIMELINE
Establish appropriate steps to be taken and develop a detailed timeline that both parties can agree upon. This process is critical to ensure faster regulatory approval. Speed can be critical for manufacturers that are playing in a competitive market.
Step Three: DESTRUCTIVE TESTING
Begin product sampling process. This is essential. Our teams go onsite to the customer factory to understand all the materials that go into the product, how it has been manufactured and how it must be installed. All this data must be gathered upfront, as in most cases, the product will eventually be destroyed for destructive testing. Destructive testing is conducted by damaging the specimen that is being tested. Materials that undergo destructive testing are damaged due to the test procedures. This process establishes both traceability and factory production control.
Step Four: QUALITY CONTROL
Certification is a long-term relationship. A product's life cycle may last for several decades, yet the customer needs might evolve over time, and we must be able to adapt to their needs quickly to keep pace with market demands. For example, products may be enhanced, key materials may no longer be available, industry regulations may change, new sustainability requirements may come into play, or a company may want to build a new plant instead of shipping its goods. In all cases, quality control is essential – we must ensure consistency across the network. With any of these changes coming into play, the inspection process is critical.
Step Five: SPEED TO MARKET
Speed to market is critical in today's competitive environment. For manufacturers that sell products in various markets around the world, requirements for certification can be very different. Markets like Southeast Florida will not be the same as the Middle East, Europe, or Southeast Asia. Intertek has a global presence, so we can discern the nuances between countries. Intertek has a presence on every continent, and in many countries, making Intertek a truly a one-stop shop. We have local teams that can help interpret the differences in requirements and ultimately save customers money by direct collaboration across our offices.
Step Six: CERTIFICATION MARK
Product certification marks indicate that a product conforms to applicable safety, quality, or performance standards and can be used in advertising, sales literature, and user documentation as a marketing aid. In most markets, conformity to local requirements is mandatory before products can be sold. Intertek's mark is recognized globally by building inspectors, building owners, and architects. We encourage our customers to highlight the fact that they work with us, as it's proof of high-quality certification – beyond the fact that it's a necessity. An Intertek mark indicates that a known independent body has tested to appropriate standards and has certified the production of a product. A mark from a reputable firm adds value, and Intertek marks are uniquely recognized worldwide.
The Intertek Directory of Building Products provides an online directory for product certifications by Intertek.
Working with Intertek on Product Certification
When it comes to building products, Intertek can certify almost anything in a building, including doors, windows, walls, ceilings, and much more. For companies looking to differentiate their products from competitive products, having a third-party certification from a globally renowned company can add instant credibility with distinction. In a world filled with natural and man-made disasters, proof of compliance is also peace of mind for the manufacturers. As a result of the pandemic, Intertek has seen growing requests for products to access different markets. A quality certification can be a critical element in growing your business.
You can also listen to our Podcast to learn more: https://www.intertek.com/building/podcast-certification/
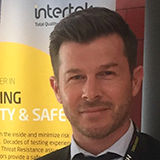
JP Kayl,
Vice President, Product Certification
Jean-Philippe has been involved with testing and certification of building products for nearly 20 years. He has developed fire testing laboratories and certification bodies in multiple countries. Jean-Philippe participated in developing building codes while also serving as a member of several standard technical panels for reaction and resistance to fire testing standards. Jean-Philippe currently heads up the global certification group for the Intertek Building & Construction business line. This group delivers and maintain compliance for 2,500+ active customers and nearly 7,000 building products manufactured all around the globe.