Validating a New Solar Factory in the U.S. from Abroad
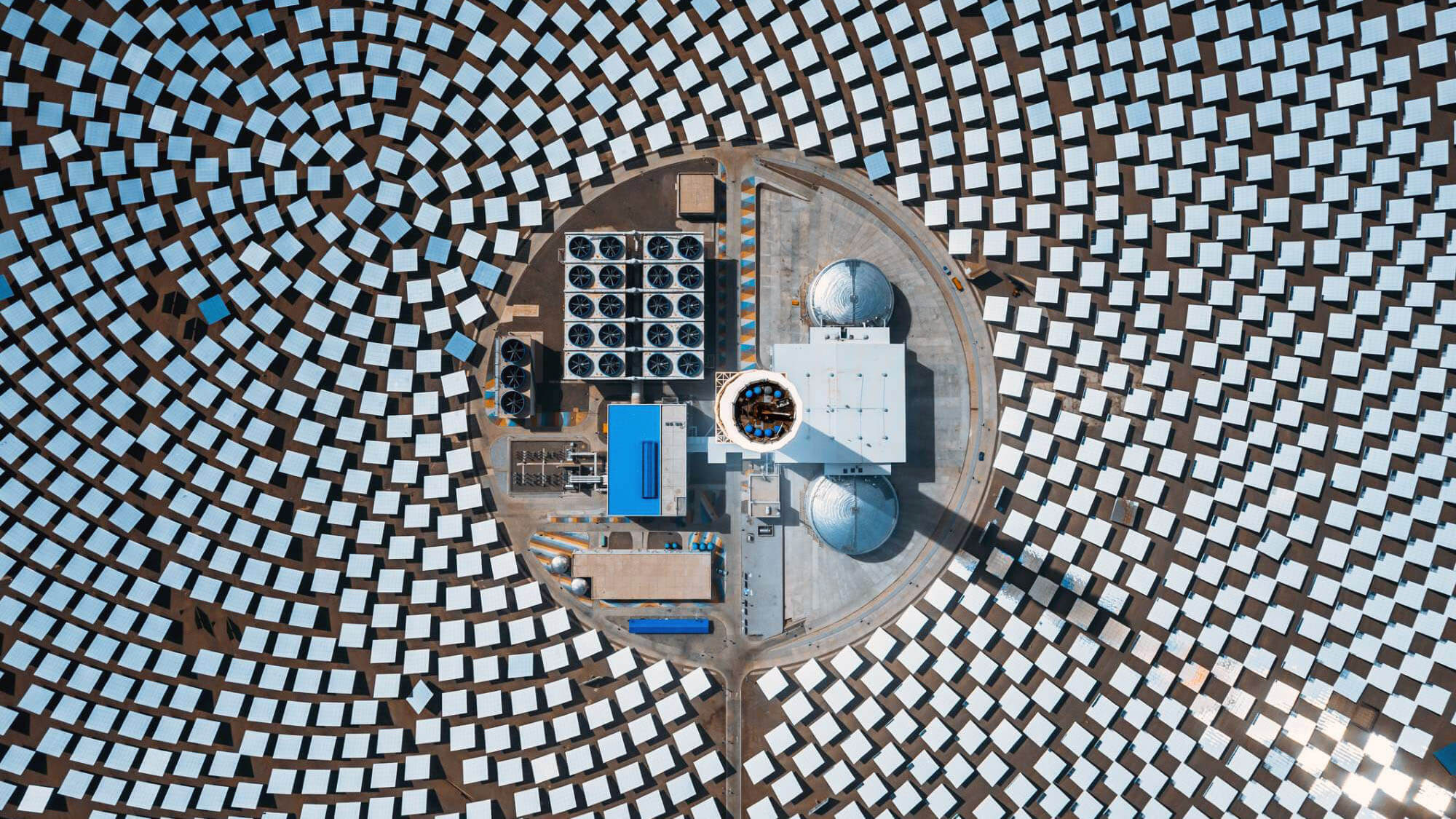
13 May 2025
What Global Manufacturers Need to Know
As the U.S. solar energy market continues to grow, manufacturers across the globe are preparing to bring their production lines and advanced equipment stateside. But before operations can begin, a critical step stands between installation and production: compliance validation.
For solar equipment built and tested overseas, entering the U.S. market introduces a unique set of safety, regulatory, and code-based challenges. Without a clear validation process, manufacturers risk costly delays, rework, or rejection from Authorities Having Jurisdiction (AHJs).
At Intertek, we support global manufacturers through a two-stage Field Evaluation process—developed to ensure a smoother, faster path to compliance and commissioning.
The Dual Path to Compliance: Preliminary and Final Evaluations
Launching a new solar factory in the U.S. requires a proactive approach. Equipment not originally built to U.S. standards needs to be evaluated before and after installation. Intertek’s Field Evaluation model helps you address both sides of the process.
Stage 1: Preliminary Evaluation in the Country of Origin
Before the equipment ships, Intertek performs a Preliminary Evaluation in its country of manufacture. This includes production machinery such as laminators, robots, conveyors, test equipment, and more. The goal is to identify compliance gaps early, allowing corrections to be made before transport.
Key benefits include:
- Avoiding delays due to noncompliance during U.S. evaluations
- Identifying safety or code issues that may trigger AHJ rejections
- Reducing last-minute redesigns or retrofits at the U.S. site
Stage 2: Final Evaluation at the U.S. Installation Site
Once the equipment is installed in your U.S. facility, Intertek’s local team completes a Final Evaluation, which includes:
- Testing and inspection based on applicable U.S. standards
- Field labeling to verify safety and compliance
- Issuance of a detailed Field Evaluation Report for AHJ approval
This final report is essential for securing AHJ sign-off and starting production operations.
The Importance of Planning Early
Field Evaluations are more than a technical requirement, they’re a strategic advantage. Many international manufacturers underestimate the differences in U.S. standards, codes and inspection procedures until it’s too late. Planning for compliance before your equipment arrives gives your team a clearer path to commissioning.
In our experience, projects that begin with a Preliminary Evaluation abroad are significantly less likely to experience delays due to compliance issues at the final installation site.
What to Expect from Intertek
With a global footprint and a coordinated approach between our international and U.S.-based experts, Intertek provides:
- Consistency from overseas assessment to U.S. labeling
- A trusted evaluation process aligned with AHJ expectations
- Quick turnaround and project efficiency—wherever you’re manufacturing
We’ve supported solar factories large and small, from single-line imports to full greenfield sites, ensuring compliance.
Final Thought
Building a solar factory in the U.S. isn’t just about logistics and installation—it’s about readiness. With Intertek’s Field Evaluations, you can bring your international equipment up to U.S. standards, streamline AHJ approvals, and move into production with confidence.