Unplanned shutdowns of oil or chemical plants can be minimized or avoided using Intertek's Risk-Based Inspection (RBI) expertise.
Intertek works with clients to implement Risk-Based Inspections (RBI), a Total Quality Assurance approach that minimizes downtime and ensures equipment longevity for oil and chemical plants. Analysis of fixed equipment, piping, pipelines, and pressure relief devices at your facility using an RBI approach can increase the effectiveness of your mechanical integrity inspection program while minimizing risk to Health, Safety and the Environment (HS&E) and maximizing resource utilization.
Key Benefits of Risk-Based Inspections (RBI):
- A more cost-effective alternative to traditional inspection, usually by means of nondestructive testing
- More reliable equipment and plant operation.
- Identification of the operational risks associated with equipment via material degradation
- Adherence to codes of compliance resulting in increased safety
- Reduction in plant downtime
Through the application of RBI analysis, process variables and materials of construction are considered to identify the type of damage that can lead to failure, where it may occur, the frequency of inspections that should take place, and appropriate and cost-effective inspection techniques. As a result, items with a high probability of failure and subsequent impact are given a higher priority for inspection than items that are of low impact, allowing for a more rational application of inspection resources. The entire process results in focusing resources on specific assets that are most likely to pose a risk to the facility.
Intertek's Risk-Based Inspection methodology and Risk Directed Mechanical Integrity Program (RDMIPTM) software continues to expand and grow as companies around the world experience the benefits associated with our world class RBI system. The program is used on all continents by large and medium sized refineries, petrochemical, and chemical facilities.
Capabilities:
We maintain a staff of recognized experts in Risk-Based Inspection; Fitness for Service; Corrosion & Metallurgy; Mechanical Integrity, Reliability, Availability, and Maintainability (RAM); and Reliability Centered Maintenance (RCM) programs and applications. Our Houston office has completed over 30 RBI projects worldwide for different clients using a variety of methodologies.
Intertek provides Risk-Based Inspection software, training, reviews, and support for client RBI programs. We also provide the personnel necessary to complete a turnkey RBI analysis program which, experience has shown, is usually the quickest and most cost-effective approach when all costs are considered. We normally suggest that clients begin with a pilot study of approximately 100 to 200 pressure vessels. Based on the results of the pilot study, you are able to evaluate the results and benefits and are provided a clear idea of the resources required to undertake a complete facility assessment.
Benefits from an Risked-Based Inspection program include improved mechanical integrity, with better identification of probable damage mechanisms. Plants with current RBI programs report an $8 to $20 return on their investment for every dollar spent to establish the program. This return is the result of improved inspection definition and associated labor and plant downtime cost benefits. We have also worked with several clients to assist them with turnaround planning using a risk based approach.
Contact Intertek to learn more about Risk-Based Inspection of chemical and petroleum facilities, and to see the Intertek RBI Qualifications Summary.
Related Engineering Services:
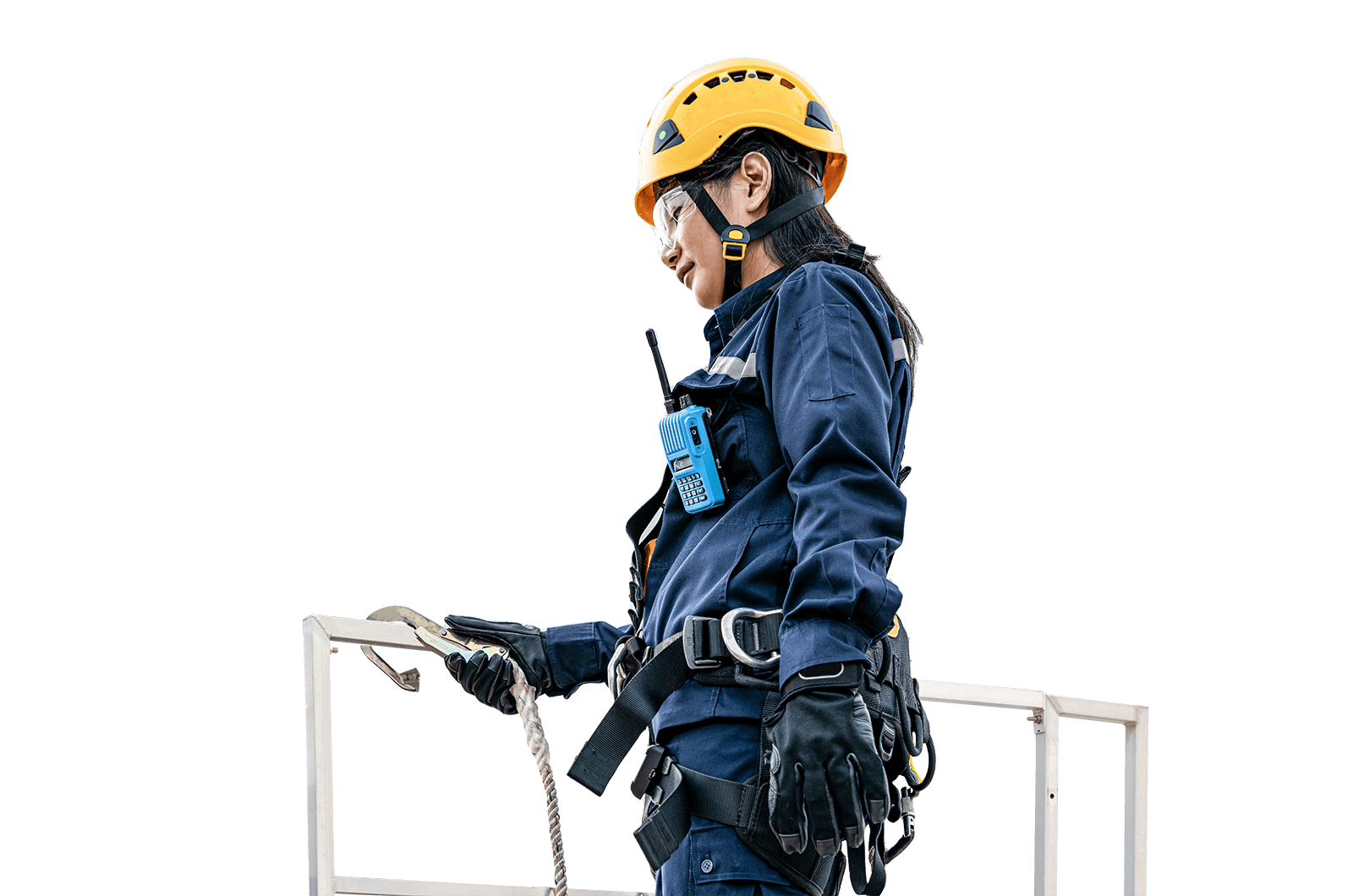