Measuring residual stress using X-Ray Diffraction
Residual stresses (RS) are internal stresses present in the material after external loading forces have been removed. Manufacturing processes such as machining, casting, alloying, quenching, cutting and tooling can contribute to a change in residual stress.
Residual stress measurements are particularly useful for quality control purposes. Determining the distribution of residual stress is important because high residual stress can lead to premature catastrophic failure of a component.
Whether you are in the transportation, medical, military, power generation or oil & gas industry, ultimately understanding residual stress can help make high-integrity products safer and more reliable and provide vital information about the performance and lifecycle management of your product.
Through our XRD unit we can:
- Help to analyse failures caused by fatigue or stress corrosion cracking (SCC)
- Estimate fatigue life and stress concentration
- Identify effects of heat treatment and surface treatments
- Provide evidence peening operations are having the desired result
- Validate manufacturing processes
- Gain an understanding of wire electrode discharge machining (EDM)
- Study surface distortion
- Process modelling and optimisation
- Provide design improvements
- Identify RS at the surface and subsurface
The benefits of choosing to measure residual stress via XRD include:
- Material removal by electro-polishing does not induce or change the stress state
- Hydrofluoric acid immersion etching facility for titanium material removal
- Non-destructive surface measurements can be evaluated without the need to section samples from large components
- Lower cost compared with Neutron and Synchrotron methods
Residual stress measurements are UKAS accredited and performed in compliance with the NPL Good Practice Guidelines.
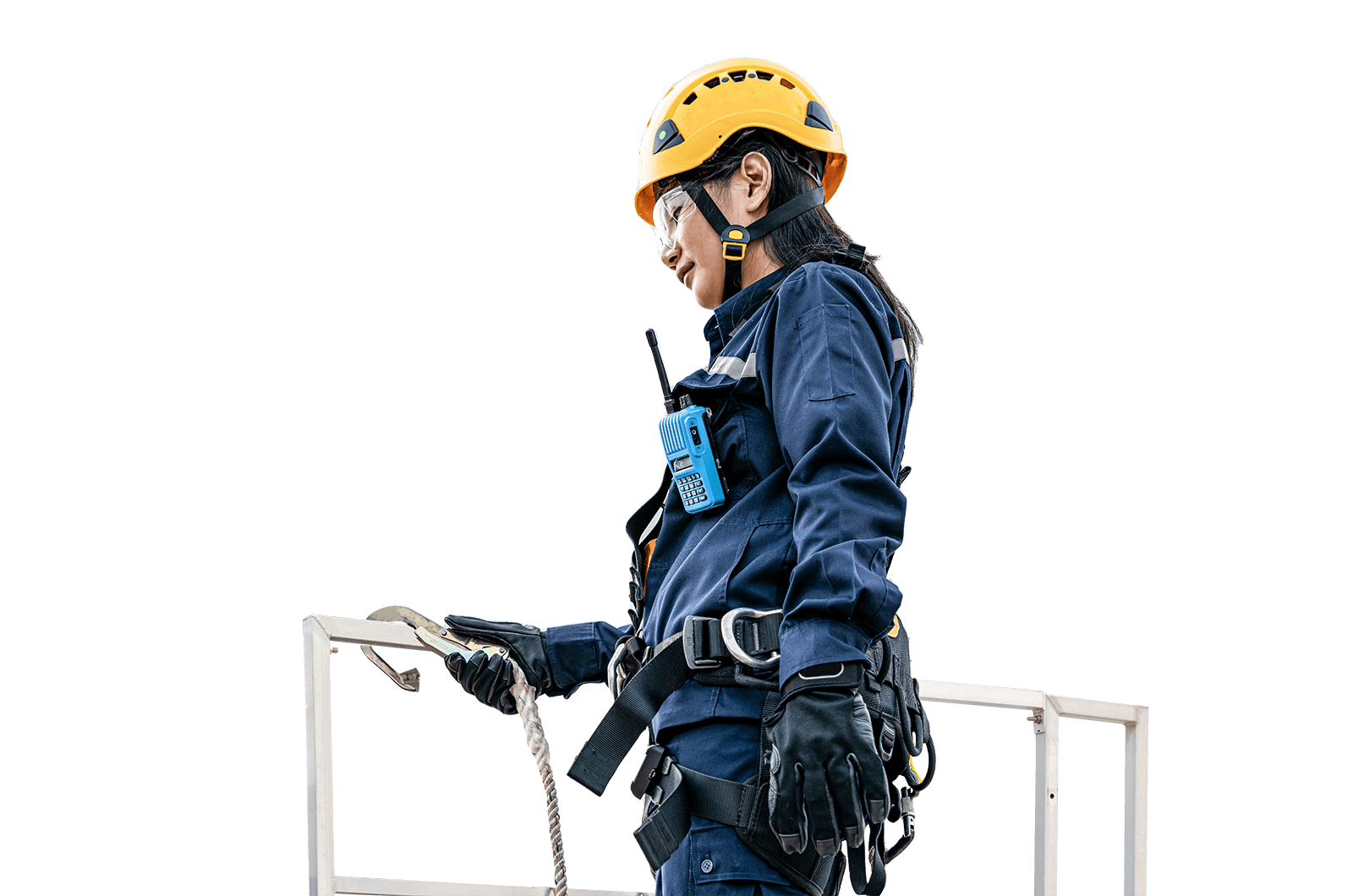